Die oberste Regel für Zwingen lautet: man kann nie genug davon haben. Meine Ergänzungsregel: wenn du glaubst, du hast genug Zwingen, dann ist deine Werkstatt zu klein.
Thomas und ich haben uns an den Eigenbau von Leimzwingen gemacht, da die mit den Mitteln eines Hobbyschreiners am leichtesten herzustellen sind.
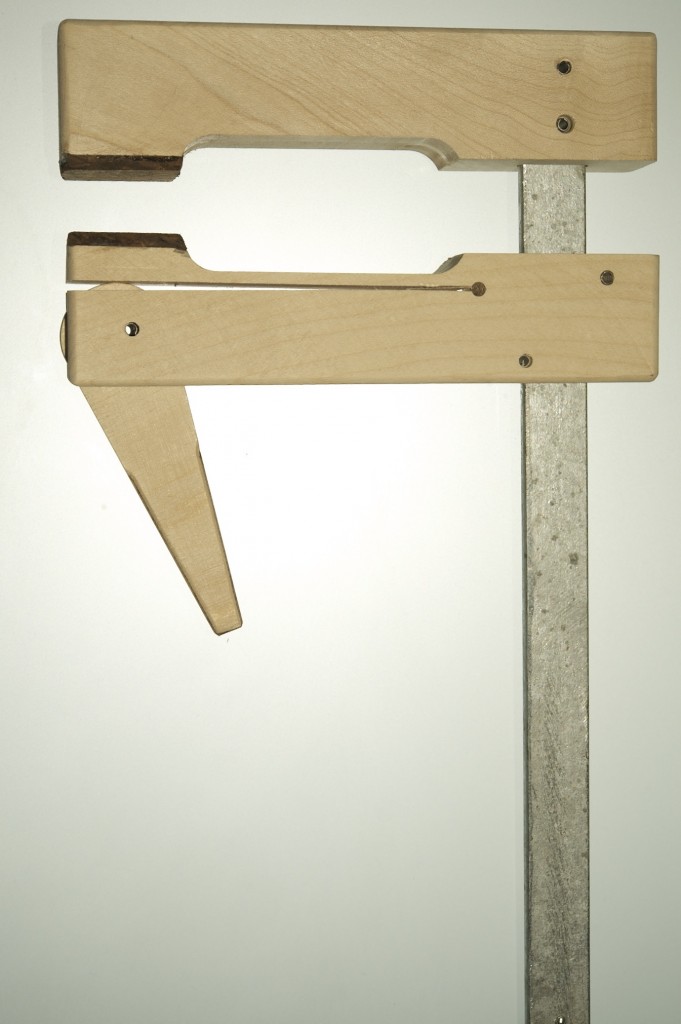
Und das sind die Einzelteile der Leimzwinge: Ahornbacken, Hebel aus Birke-Multiplex, Hohlsplinte und entweder Blindniete oder kleine Schrauben als Schutz vor dem Herunterfallen der unteren Backe.
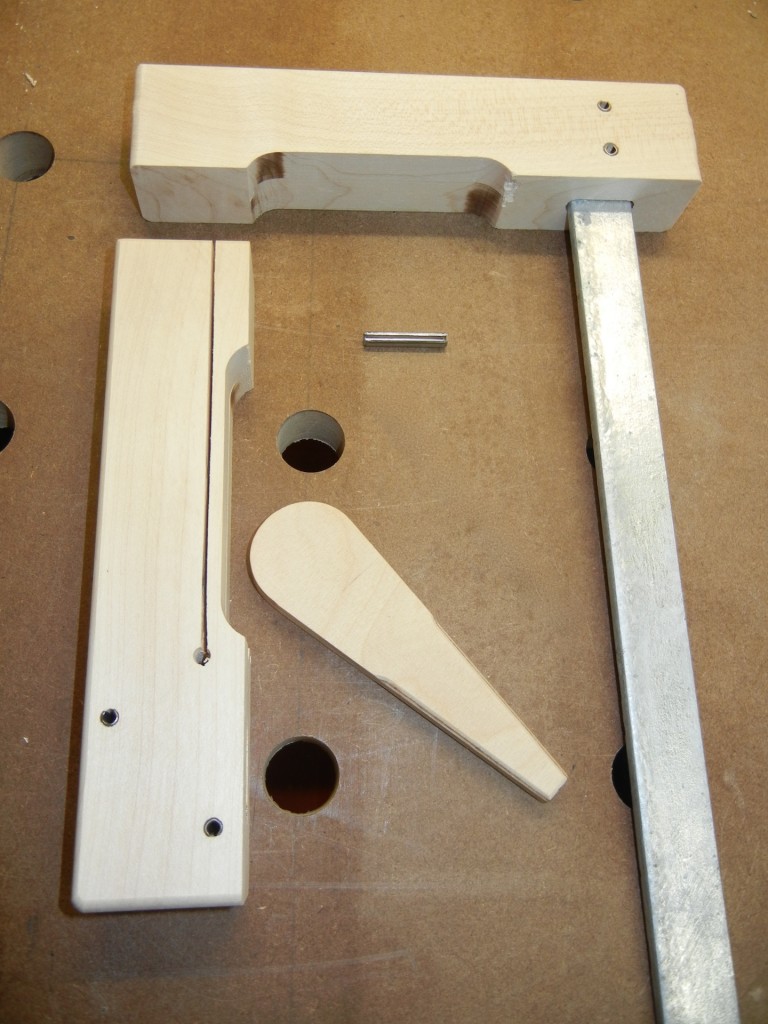
[table id=psb_lzw /]
Wofür kann man Leimzwingen verwenden?
- Sie halten stumpf auf einander geleimte Korpusteile
- Sie fixieren Korpusteilen mit Flachdübelverbindung
- Dank des Hebels und der losen Backe lassen sie sich schnell öffnen und schließen
- Sie eignen sich gut als Anschlag weil sie Quaderform haben
Wofür sind Leimzwingen nicht geeignet?
- Für Verbindungen mit langen Dübeln
- Dort wo sehr hoher Anpressdruck benötigt wird
Und die wichtigste Frage: lohnt sich der Selbstbau überhaupt? Dazu muss man wissen, dass der Aufwand für eine einzelne Zwinge sehr hoch ist. Es lohnt sich also nur die Massenfertigung. 20 Stück sollten es mindestens sein, damit sich die Serienfertigung mit den vielen Maschineneinstellungen rentiert.
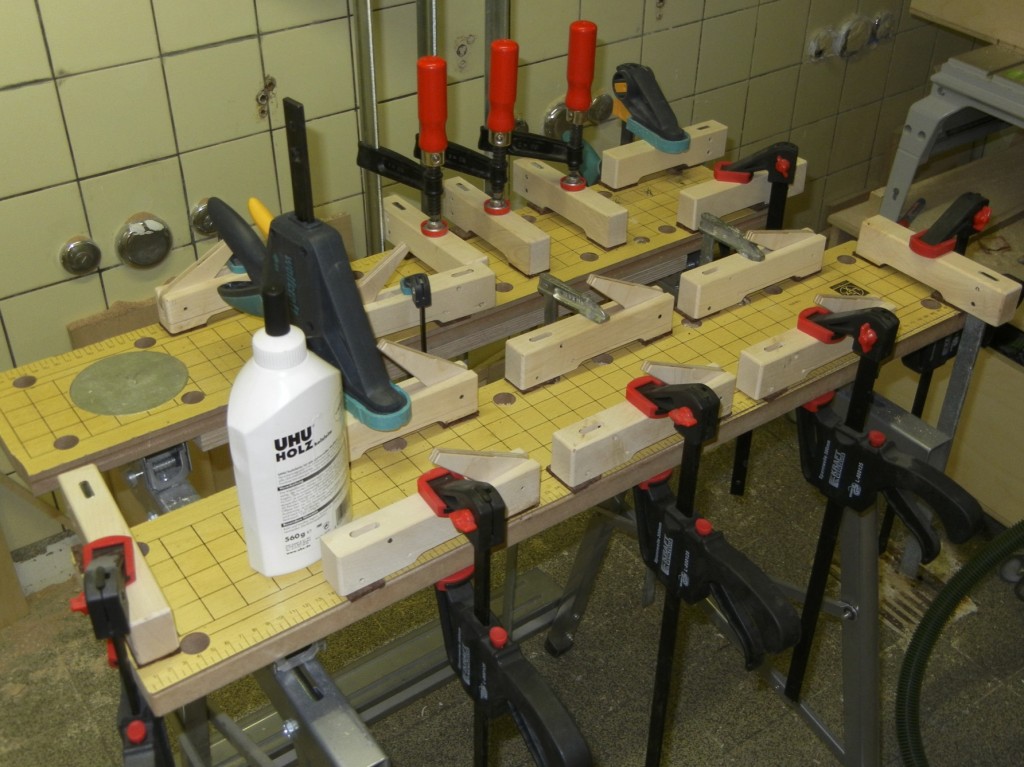
Rohmaterial
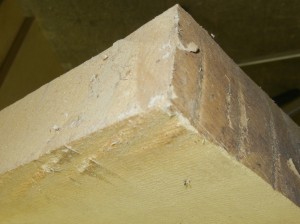
Damit die Spannbacken später stabil sind, kauften wir rohe Ahornbretter mit etwas mehr als 5 Zentimeter Dicke. Sägerau und mit Waldkante, so wie es aus dem Sägewerk kommt — nur ordentlich getrocknet. Bretter mit stehenden Jahresringen sind schwerer zu bekommen und kosten mehr, aber die Stabilität ist es wert.
Vorbereitung
Als Erstes stellten wir die Spannbackenrohlinge her. Das geht mit viel Geduld mit der Tischkreissäge alleine. Wer eine Abrichte und einen Dickenhobel sein Eigen nennt, der hat es aber bedeutend einfacher. Haben wir aber nicht.
Dazu braucht man eine gerade Bezugskante die wir auf dem Sägeschlitten geschnitten haben. Die Waldkante sollte man dabei großzügig abtrennen, denn das wirklich stabile Holz liegt weiter innen. Als nächstes schneidet manr am Paralleanschlag 35 mm breite Streifen aus dem Brett. Wenn das Brett noch sägerau und nicht gehobelt ist, muss man darauf achten, dass es nicht auf Unebenheiten kippt, sondern mit der Bezugskante press am Anschlag lag. Das hat bei uns erstaunlich gut funktioniert.
Dann werden die Streifen abgelängt. Äste, Risse und andere Imperfektionen müssen beim Ablängen entfernt werden. Sie würden später sonst der Stabilität der Spannbacken schaden.
Wenn alles gut gelaufen ist, hat man jetzt Die Backenrohlinge. Die sollten saubere rechte Winkel aufweisen.
Spannbacken herstellen
Die nächsten Schritte beschreiben, wie aus den Rohlingen die Spannbacken werden.
Ausschnitt für den Spannhebel
Wenn die Tischkreissäge schon mal steht, dann kann man auch gleich die Aussparung für den Hebel machen. Dabei nutzt man aus, dass die Aussparung am hinteren Ende rund werden muss. Alternativ geht das auch mit dem Frästisch, sieht aber nicht so schön aus, weil die Rundung in der Aussparung dann fehlt.
Mehrere Schnitte mit der Kreissäge am Längsanschlag werden so nebeneinander gesetzt, dass eine 9 mm breite Nut entsteht. Heikel ist, dass man das Werkstück nicht durchschieben darf.
Wir haben daher die Zugfunktion der Säge verwendet und das Werkstück auf der Säge festgespannt. Wer keine Zugfunktion hat, muss sich einen anderen Trick einfallen lassen. Die Gefahr beim Zurückziehen des Werkstücks im Mitlauf ist nicht unerheblich! Vorsicht walten lassen.
In die 9 mm Nut wird später der Hebel aus Multiplex eingesetzt.
Rückenführung
Sowohl die obere als auch die untere Spannbacke brauchen eine Aussparung zwischen Rücken und Spannfläche, die dafür sorgt, dass die Backe nur am vorderen Ende Druck aufbauen muss.
Wir haben die Aussparung auf dem Frästisch hergestellt. Das ging nachdem die Anschläge eingestellt waren ganz fix. Da es hier nicht so genau geht, wäre eine Bandsäge auch in Ordnung. Eine Stichsäge dürfte dagegen mit dem engen Radius am Ende in einem Hartholz nicht zurecht kommen.
Als nächstes stellt man die Durchführungen für den Stahlrücken her. An der oberen Backe muss das ausgefräste Loch stramm auf dem Rücken sitzen. Hier soll sich später nichts mehr bewegen können. Das heißt, man fräst mit einem 5 mm Fräser ein Langloch, bei dem die Zentren der vorderen und hinteren Fräserposition genau die Rückendicke auseinander sind. Im Zweifelsfall lieber langsam herantasten.
Die untere Backe soll später beweglich sein. Dort muss das Langloch zwei Millimeter länger sein, sodass die Backe beim Verschieben auf dem Rücken ein bisschen nach vorne und hinten kippen kann. Auch seitlich sollte gerade soviel Luft sein, dass sich die Backe leicht verschieben lässt ohne seitwärts zu wackeln.
Ein wichtiger Tipp, den Thomas und ich auf die harte Tour gelernt haben ist, dass man die Backen beim Umdrehen immer mit der gleichen Längsseite am Anschlag anlegen muss. Es ist besser, wenn an der schmalen Seite des Langlochs ein kleiner Versatz übrig bleibt als an der breiten. Sonst sitzt später die Backe seitlich gekippt. Das obere Langloch sollte gerade so lang sein, dass mit leichten Hammerschlägen die Backe auf den Rücken gebracht werden kann. Unten sollte das Langloch auf beiden Seiten je einen Millimeter Spiel zu Rücken aufweisen bevor die Rundung beginnt. Zwei Hohlsplinte hindern später die Backe daran, dem Druck nachzugeben.
Anschließend kann man die Außenkanten noch mit einem Abrundfräser bearbeiten. Die Zwinge liegt dann einfach schöner in der Hand.
Spannzunge ausschneiden
Der einfache Teil war die Entlastungslöcher herzustellen. Tischbohrmaschine mit zwei Anschlägen richtig eingestellt, und alle Löcher nach einander gebohrt. Die Entlastungslöcher dienen später dazu zu verhindern, dass die Zunge beim Festzwingen entlang des Schnitts weiter reißt.
Als unerwartet schwierig hat sich das Ausschneiden der Spannzunge an der unteren Backe erwiesen. Thomas’ erster Versuch mit der Bandsäge scheiterte daran, dass das Sägeblatt in dem sehr harten Ahorn einfach nicht geradeaus sägen wollte. Schon garnicht in akzeptabler Geschwindigkeit. Ich schätze, ein richtig teures Profigerät hätte das geschafft, aber das Motto lautet nun mal: Hobby.
Die Kreissägeblätter unserer Sägen hätten einen viel zu breiten Schnitt hinterlassen und schieden damit aus. Zum Handsägen waren wir zu faul. Das hätte auch der Idee der Serienfertigung widersprochen.
Dank eines sehr kleinen Kreissägeblatts und Thomas’ weit herunter regelbarer Oberfräse konnten wir uns eine kleine Vorrichtung bauen, die zum Erfolg geführt hat.

Wir mussten nur die Endanschläge passend verschieben bevor wir die zweite Seite gesägt haben. Den kleinen Rest, der dadurch übrig blieb, dass das runde Blatt eben auch einen runden Ausschnitt im Holz hinterlässt, hat Thomas mit der Handsäge bis zur Entlastungsbohrung durchtrennt.
Klemmhebel
Der Klemmhebel ist eine simple Konstruktion. Erst sägt man Dreiecke aus 9 mm Birkensperrholz aus. Die Dreiecke haben einen Winkel von 15°. Dann schneidet man die Rundung am breiten Ende. Thomas hat das ganz fix mit einer Schablone und einem Bündigfräser am Frästisch erledigt. Die schmale Seite kann man mit einem Abrundfräser noch verbessern. Sie fasst sich dann beim Gebrauch angenehmer an. Wichtig ist, dass man das Achsloch an die richtige Stelle setzt. Der Hebel ist ein Exzenter, sonst funktioniert die Leimzwinge später nicht.
Montage
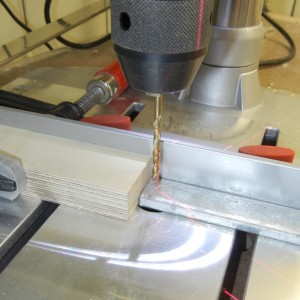
Wenn alle Teile geschnitten und alle Löcher gebohrt sind, dann ist der Zusammenbau ganz simpel. Das Wichtigste ist, die Hohlsplinte mit der geschlossenen Seite in Belastungsrichtung eingeschlagen werden. Die Hohlsplinte in der oberen Backe zeigen mit der Öffnung nach oben, in der unteren Backe zeigt die Öffnung weg vom Rücken. Der Hohlsplint für den Hebel zeigt weg von der Zunge.
Damit später die Hohlsplinte für die obere Backe perfekt sitzen, setzt man die fertige Backe zuerst oben bündig auf den Rücken. Dann bohrt man mit einem Metallbohrer erst die durch die Hälfte der Backe, dann vorsichtig durch den Rücken, dann durch den Rest. Es empfiehlt sich, den Holzspan vom Bohrer zu entfernen bevor man weiter durch den Rücken bohrt.
Wenn die obere Backe fixiert ist, wird die untere Backe einfach auf den Rücken geschoben. Ein kurzer Test kontrolliert ob die Backe sich leicht bewegen lässt und nicht bei Druck nach unten nachgibt. Wenn das in Ordnung ist, dann fehlt nur noch die Bohrung man Rückenende und der Blindniet, der die untere Backe am Herunterfallen hindert.
Schutzbacken
Traditionell sind die Schutzbacken von Leimzwingen aus Kork. Leder oder ein robuster, rutschfester Kunststoff wäre auch eine Option. Den Kork haben wir mit einem Teppichmesser auf leichtes Übermaß geschnitten, mit Weißleim verklebt und schließlich vorsichtig den Überstand mit Schleifpapier bündig geschliffen. Dabei sollte man immer zum Holz hin schleifen, damit der Kork nicht ausreißt.
Hallo, lieber Sebastian, lieber Thomas
Wunderbar, wie der Eigenbau von Leimzwingen beschrieben ist. Man kann alles ganz gut gedanklich nachvollziehen. Und alle Fachausdrücke sind entnommen aus der Fachsprache des Schreinerhandwerks?
Nur weiter so.
Johannes
Besten Dank. Ja, auch wenn es natürlich für uns nur ein Hobby ist versuchen wir die korrekten Begriffe aus dem Schreinerjargon zu verwenden. Ist leichter verständlich, wenn alle die gleichen Begriffe benutzen.
Hallo, super Projekt! Kurze frage: wieso 32mm lange Hohlsplinte bei 28mm breiten Backen? VG Manuel
Thank you for sharing your knowledge so clearly with the pictures, it eas clearly & easy to understand from & an old man who is trying to become a lot better at my woodworking projects.